石油地面设备数字孪生:油气田的智能变革密码
一、石油工业的 “数字分身”
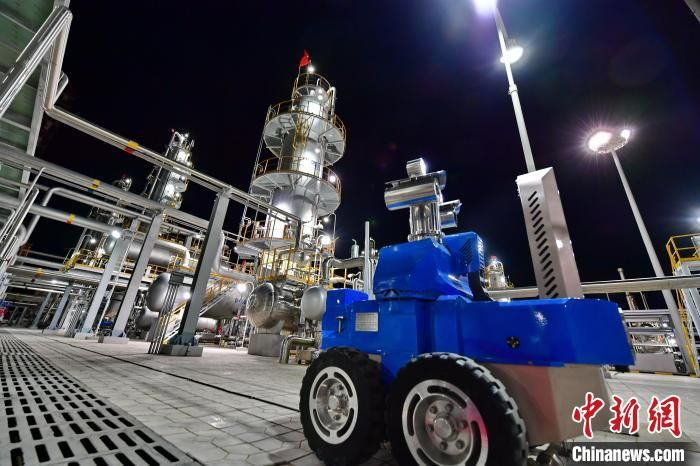
石油,作为现代工业的 “血液”,其重要性不言而喻。然而,石油行业面临着诸多棘手挑战。从勘探开采环节看,随着易开采资源逐渐减少,新油源往往藏于深海、地层深处等极端环境,开采难度飙升,成本也随之水涨船高;地缘政治因素像颗不定时炸弹,产油地区局势稍有波动,全球石油供应和价格便会掀起惊涛骇浪。在加工与使用阶段,大量温室气体和污染物排放,让石油行业成为环保舆论的焦点,各国严苛法规接踵而至,企业减排压力山大;与此同时,新能源发展势头迅猛,电动汽车普及等因素,使得石油在能源市场的份额遭遇强劲对手,竞争白热化,价格还像坐过山车般起伏不定。
在这样的困境下,数字孪生技术宛如一道曙光映入石油人的眼帘。简单来说,数字孪生就是为物理实体在虚拟世界打造一个超逼真的 “数字分身”。这个分身可不简单,它依托物联网、大数据、人工智能等前沿技术,与现实中的石油设备、生产流程实时同步数据,全方位模拟其运行状态。就好比给石油工业戴上了一副拥有 “透视眼”“预见力” 的智能眼镜,无论是设备的细微故障隐患,还是生产流程的优化方向,都能尽收眼底、提前掌控。对于石油地面设备,从巨型抽油机到错综复杂的输油管道,数字孪生都有潜力让它们的管理运维实现质的飞跃,开启石油工业智能化新篇章。
二、数字孪生究竟是什么?
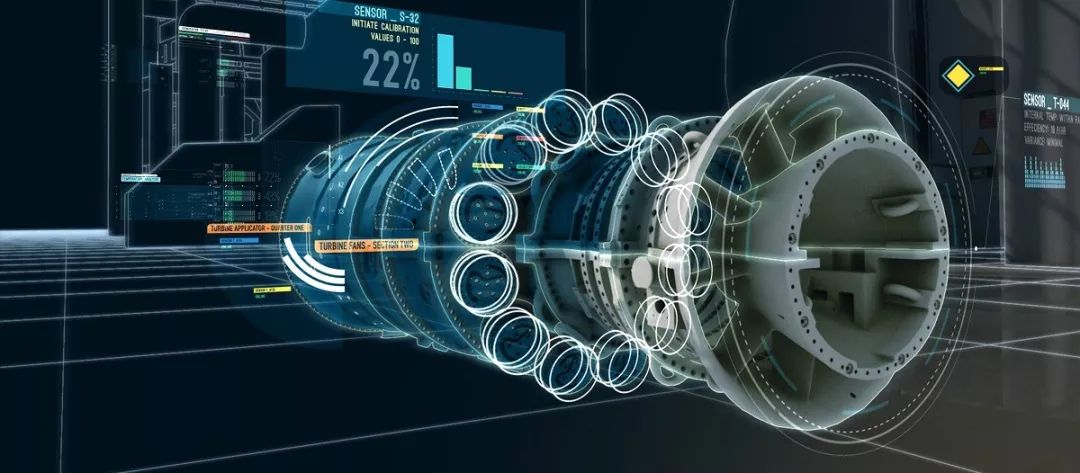
(一)概念解读
数字孪生,简单来讲,就像是给现实世界的物体或系统创造一个在虚拟世界里的 “双胞胎兄弟”。这个虚拟的 “兄弟” 可不只是徒有其表,它依托一系列前沿科技,与现实中的原型实时共享数据,从外观模样到内在性能,全方位复刻。以油气田的抽油机为例,现实中的抽油机在旷野中不停 “点头” 抽油,数字孪生体则在计算机系统里同步模拟它的一举一动,大到机械臂的摆动幅度、电机的运转功率,小到一个螺丝的受力情况,任何细微变化都能精准映射,实现虚拟与现实的深度交融、实时互动。
(二)工作原理大揭秘
对于油气田地面设备,数字孪生的搭建宛如一场精细的 “克隆工程”。首先,要利用三维建模、地理信息系统(GIS)等技术,依据油气田详细的设计图纸、实地测绘数据,构建出与真实场景丝毫不差的虚拟模型,涵盖抽油机、输油管道、储油罐等各类设施,连它们之间的空间布局、相对位置都精准还原。紧接着,通过密布在设备上的传感器 “大军”,温度传感器感知设备发热状况,压力传感器监测管道内部压力,振动传感器捕捉机械运行的振动频率等,这些传感器如同敏锐的 “神经末梢”,将采集到的海量数据,借助高速稳定的物联网通信,源源不断传输至数据处理中心。数据中心对数据进行清洗、整合后,驱动虚拟模型实时运转,最终让虚拟模型与现实设备状态实现毫秒级同步,现实中设备一有风吹草动,虚拟模型立刻反馈,为运维人员提供精准决策依据。
(三)关键技术支撑
数字孪生背后是一群 “技术担当” 在发力。建模技术是 “塑形师”,像计算机辅助设计(CAD)、建筑信息模型(BIM)等,为油气田地面设备打造出结构、外观高度仿真的数字躯体;物联网技术充当 “神经脉络”,数以千计的传感器、智能仪表、无线通信模块等,确保物理设备与虚拟模型之间数据传输通畅无阻;大数据技术扮演 “智慧大脑”,面对从油气田各处涌来的海量、多源、异构数据,进行存储、管理、分析,挖掘出隐藏在数据背后设备运行的规律与潜在问题;人工智能技术则是 “智能参谋”,机器学习算法基于大数据学习设备正常与故障状态特征,实现故障自动诊断、预测性维护,比如提前预判抽油机可能出现的机械故障,辅助工作人员提前维修,防患于未然。
三、数字孪生在石油地面设备的卓越应用
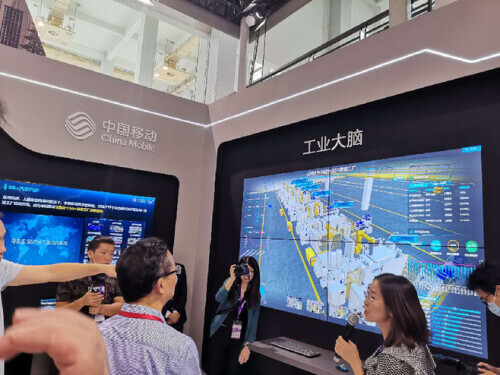
(一)精准建模与仿真
油气田地面设施分布广袤,从绵延数千米的输油管道到林立的抽油机、庞大的储油罐,传统二维图纸难以全方位展现其复杂全貌。数字孪生技术打破这一局限,运用高精度三维建模,依据详实地理信息、设备参数,为油气田打造 1:1 虚拟模型。技术人员轻点鼠标,就能如置身实地般穿梭其中,查看每处细节。如在新油气田开发设计阶段,利用数字孪生模型模拟不同开采方案,精准预测产量、能耗、设备寿命,对比择优。面对复杂地质条件,模拟地震、地层沉降对地面设施影响,提前加固脆弱部位,防患未然。还可虚拟演练极端天气、设备突发故障场景,制定应急预案,提升应急处理能力,让油气田从容应对各类挑战。
(二)设备维护 “未卜先知”
以往石油设备维护多是定期巡检、事后维修,耗时费力且易造成生产中断。数字孪生彻底革新这一模式,通过传感器网络实时 “凝视” 设备状态,温度、压力、振动等数据源源不断汇入孪生模型。一旦数据偏离正常区间,系统立即报警。更厉害的是,基于大数据分析和机器学习算法,它能依据历史数据、同类设备故障案例,提前精准预测潜在故障,给出维护建议。某海上油气平台引入数字孪生后,成功提前 3 天预测关键泵机轴承磨损故障,及时维修,避免数百万美元停产损失,保障油气稳定输送,运维成本降低近 20%,真正实现从 “被动救火” 到 “主动预防” 转变。
(三)生产流程智能优化
油气生产流程环环相扣,任何环节卡顿都会引发连锁反应,降低效率。数字孪生成为优化生产流程的 “智能军师”,实时采集各环节数据,从油井出油量、成分到管道输送压力、流速,再到炼化环节温度、化学反应进程,全方位掌控。利用这些数据,建立智能调度模型,依据市场需求、油价波动,动态调整开采量、优化油气调配路径、合理安排炼化产能。在某大型陆地油气田,数字孪生助力优化生产流程后,油气采收率提升 8%,能源消耗降低 10%,整体生产效率提高 15%,在激烈市场竞争中脱颖而出,经济效益显著提升。
四、优势尽显,效益飙升
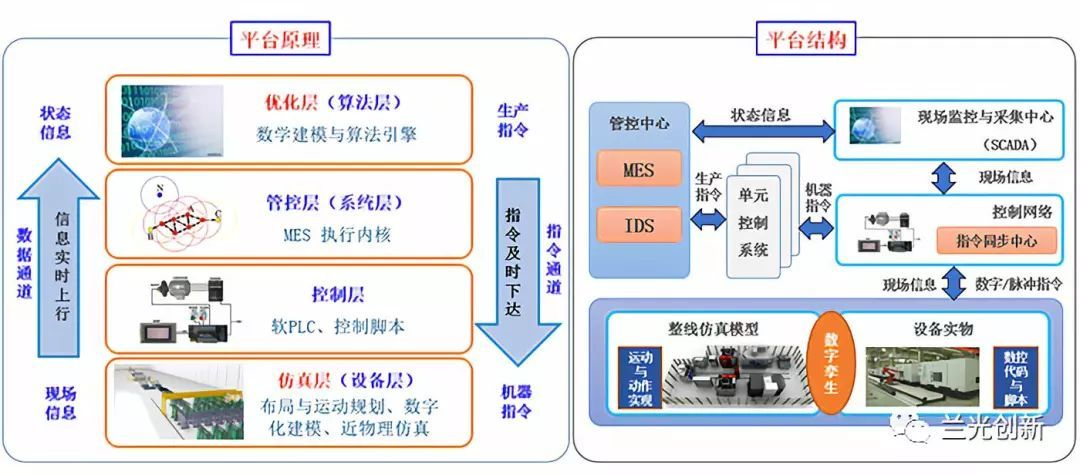
(一)降本增效看得见
在石油开采领域,数字孪生技术的应用带来了显著的成本优化。以往,油田巡检依赖人工,工人需穿梭于广袤油区,耗费大量人力、物力与时间,且难以实时发现隐蔽故障隐患。引入数字孪生后,通过远程实时监控与智能诊断,人工巡检频次大幅降低,人力成本削减约 30%。以某大型陆上油田为例,以往每月人工巡检成本高达 50 万元,应用数字孪生后,降至 35 万元。同时,设备故障预测性维护准确率超 90%,将非计划停机时间从年均 200 小时骤减至 50 小时以内,极大提高生产连续性,每年因减少停产损失带来的额外收益超千万元,真正实现降本与增效 “双丰收”。
(二)决策支持更科学
对于石油企业管理层,数字孪生提供全方位、精准的数据洞察,成为决策 “智囊团”。在制定油气田开发方案时,传统模式仅凭经验与有限数据估算,风险高、不确定性大。如今,借助数字孪生的虚拟模型,结合地质数据、历史开采数据、市场动态等海量信息,进行多方案模拟对比。如某海外油气项目,计划开拓新油区,利用数字孪生模拟不同开采速度、技术应用、市场价格波动下的经济效益,精准筛选出最优方案,投资回报率预估提升 15%,为企业战略投资决策筑牢根基,有效规避盲目投资风险,引领企业稳健前行。
(三)安全保障再升级
石油生产环境高危,安全乃重中之重。数字孪生为安全生产铸就坚固防线,通过实时监测设备运行、环境参数,如油气管道压力、炼油装置温度等,利用智能算法即时捕捉异常波动,第一时间揪出安全隐患。更能模拟火灾、爆炸、泄漏等事故场景,依据模拟结果优化应急预案,明确人员疏散、抢险救援最优路径。某石化厂引入数字孪生安全系统后,安全事故发生率降低 60%,事故应急响应时间从半小时缩至 10 分钟以内,将潜在损失降到最低,为员工生命安全、企业平稳运营保驾护航。
五、落地难题与破解之道
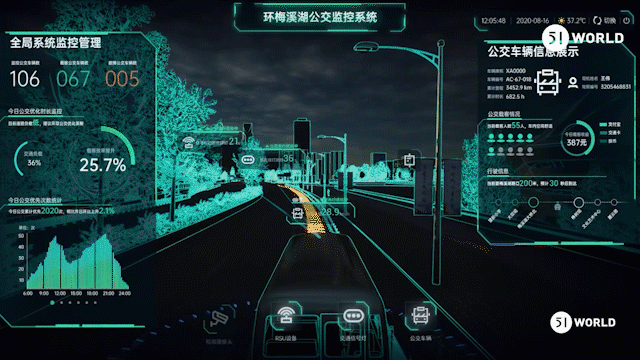
(一)数据困境
石油行业历史悠久,设备与流程积累海量数据,但数据质量参差不齐,部分老旧设备传感器精度差、数据缺失或错误频发,像服役数十年的抽油机,传感器常因恶劣环境干扰,传输数据波动剧烈,难以为数字孪生模型提供精准 “养分”。同时,数据安全与隐私保护如高悬达摩克利斯之剑,油气田生产涉及国家能源关键信息、企业商业机密,一旦泄露,后果不堪设想。并且,从偏远油气井到数据中心,数据采集与传输面临偏远地区网络信号弱、传输带宽窄等难题,大量实时数据难以及时 “回传”,阻碍数字孪生系统实时性优势发挥。
为攻克这些难关,一方面,行业需统一数据标准规范,对各类设备数据格式、精度、采集频率等详细界定,像为石油数据制定 “度量衡”;定期校准、维护传感器,提升数据源头质量。另一方面,加强数据加密保护技术研发应用,从数据存储、传输到使用全流程加密,引入区块链等新技术,确保数据不可篡改、可追溯;优化数据传输网络,利用卫星通信、5G 专网等手段,拓宽偏远地区数据传输 “高速路”,保障数据实时畅达。
(二)技术瓶颈
数字孪生模型精度提升困难重重,油气田地下地质结构复杂、地面设备多样,精准模拟需考虑海量因素,微小参数偏差就可能让模型与现实 “谬以千里”,如模拟油藏渗流,地层渗透率细微变化就会大幅影响开采预测结果。实时性也是一大挑战,油气生产动态变化,要求数字孪生模型毫秒级同步现实,可复杂计算、大规模数据处理常使模型更新滞后。此外,数字孪生横跨多学科,涵盖石油工程、计算机科学、数学等,各学科知识深度融合难,不同专业人员沟通协同存在 “壁垒”,制约技术创新突破。
应对这些挑战,企业与科研机构要加大研发投入,设立专项攻关项目,如联合高校开展 “高精度油气田数字孪生模型研发” 课题;积极引入前沿算法,像量子计算辅助复杂模型快速求解,提升模型精度与运算速度。同时,搭建跨学科交流平台,举办学术论坛、行业研讨会,促进石油工程师、数据科学家、软件开发者深度对话,打破知识隔阂,碰撞创新火花,合力攻克技术难题。
(三)人才短缺
石油行业传统人才集中于地质勘探、采油工程等领域,熟悉数字孪生技术的复合型人才稀缺。这类人才既要懂石油专业知识,掌握油气田开采、储运流程细节,又需精通建模、编程、数据分析等数字技能,能玩转数字孪生技术 “十八般武艺”。人才培养体系也不完善,高校相关专业课程设置滞后,重理论轻实践,学生毕业后难以快速上手复杂项目;企业内部培训缺乏系统性、针对性,难以满足数字孪生技术快速发展需求。
为填补人才缺口,高校应与时俱进优化专业课程,打造 “石油 + 数字孪生” 跨学科培养方案,增加实践教学比重,与企业共建实习基地,让学生在项目实战中成长。企业要强化内部培训体系,邀请外部专家、技术骨干授课,定制个性化培训课程;积极从互联网、科技企业等外部引入数字人才,组建跨领域创新团队,用 “引育结合” 策略打造数字孪生人才梯队,为石油地面设备数字孪生发展注入持久动力。
六、未来已来,前景无限
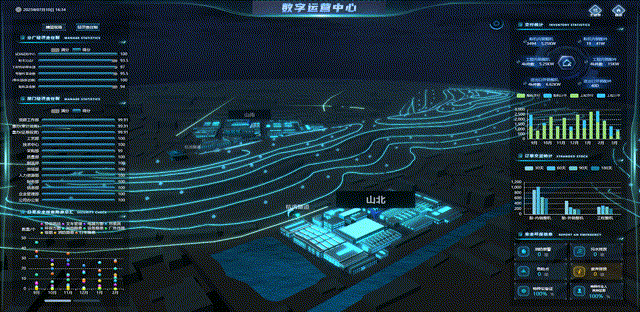
展望未来,数字孪生在石油地面设备领域前景一片光明。一方面,它将与 5G、区块链、量子计算等前沿技术深度融合,5G 超高速率、超低时延赋能数字孪生模型实时数据交互,让操控如丝般顺滑;区块链保障数据可信共享,为跨企业、跨国界能源合作筑牢根基;量子计算助力复杂模型秒级求解,解锁前所未有的精度与效率。另一方面,应用场景持续拓展,从常规油气田迈向页岩气、可燃冰等非常规能源开采,深入油藏数值模拟、提高采收率方案优化等核心环节,甚至延伸至能源交易、碳足迹追踪等领域,助力石油行业全产业链数字化转型。可以预见,随着持续创新与广泛应用,数字孪生必将重塑石油地面设备运维管理模式,推动石油行业迈向智能化、可持续发展的新纪元,成为全球能源版图变革的关键力量。
本文版权归网站所有,转载请联系并注明出处: